Welcome to the cable production of LAPP! The Stuttgart-based company stands for reliable connectivity solutions. In addition to connectors and drag chains, these include cables and wires in particular, which LAPP has been manufacturing and selling since 1959.
Every day, thousands of kilometers of different cables are produced in LAPP’s production facilities. In the Stuttgart company’s largest plant alone, in Forbach, France, 130,000 kilometers of cable are produced each year; this corresponds to a daily output the length of the route from Stuttgart to Berlin. In total, LAPP produces at 25 production sites in 15 countries. Each plant has a different focus, among other things adapted to local market needs. The cable plant in Stuttgart, for example, primarily manufactures connection and control cables with lower volumes and greater variety. CEAM in Italy specializes in data cables, while Lapp Muller in France concentrates on project business and marine. The two production plants in India mainly manufacture data cables and infrastructure cables and tend to be designed for large volumes and great variety. Korea specializes in radiation crosslinked cables. And in the USA, the focus is once again on connecting and control cables.
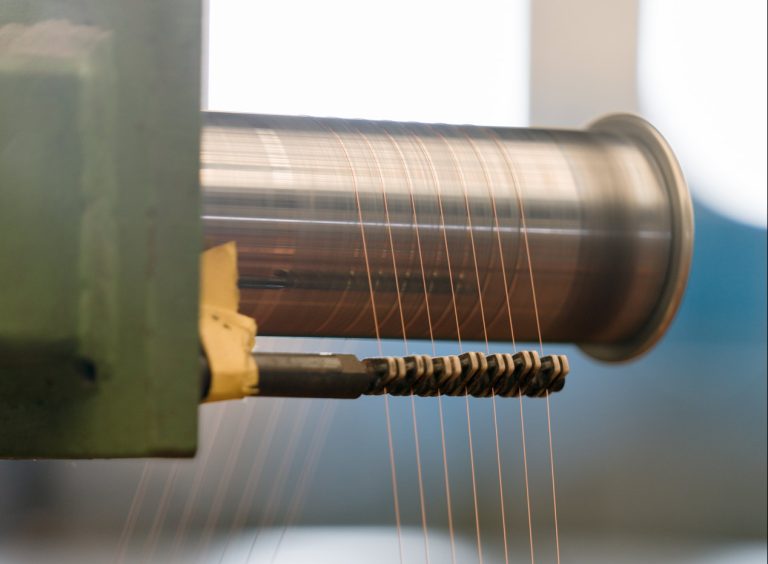
From copper wire to a high-quality cable
But how exactly do we get to the end result now, a durable and flexible cable? “First of all, we select the right raw materials for the cable to be manufactured,” explains Joachim Schmid, Managing Director of Stuttgarter Kabelwerke. “We then use them to equip the plant.” Depending on the planned end result, the prescribed parameters are set on the machines. Cable production is highly individual – plastics can react very differently to heat, cold or humidity. Therefore, sensitivity and know-how are essential for the machine and system operators even in this first step.
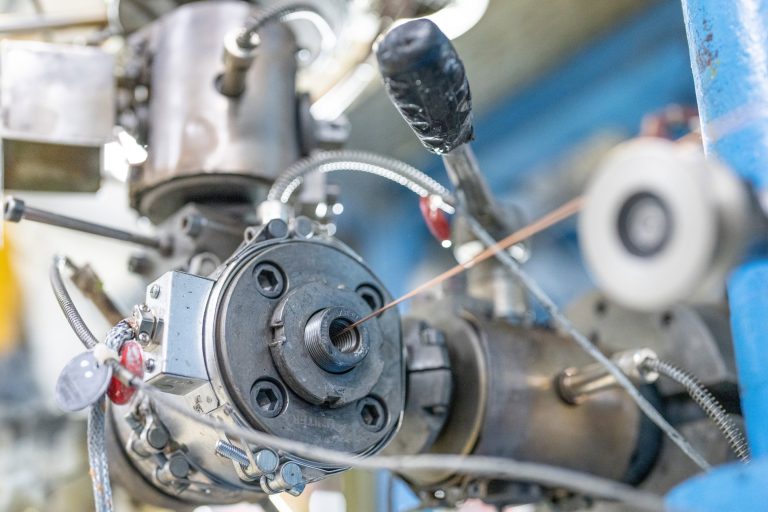
Equally important are the copper strands. Copper is an excellent and durable conductor. Its soft texture also makes it a metal that is easy to work with, resistant and ductile. Before the finished strand drums are delivered to Stuttgart, copper ingots must first be drawn over drawing machines. Using diamond drawing irons, the blocks are ground into thin wires that can be further processed at LAPP. During the so-called stranding process, different strand classes can be defined. These determine the flexibility of the cable. In the production in Forbach, LAPP has its own copper train. This saves costs in production and ensures that this production step also meets the high quality standards of the products.
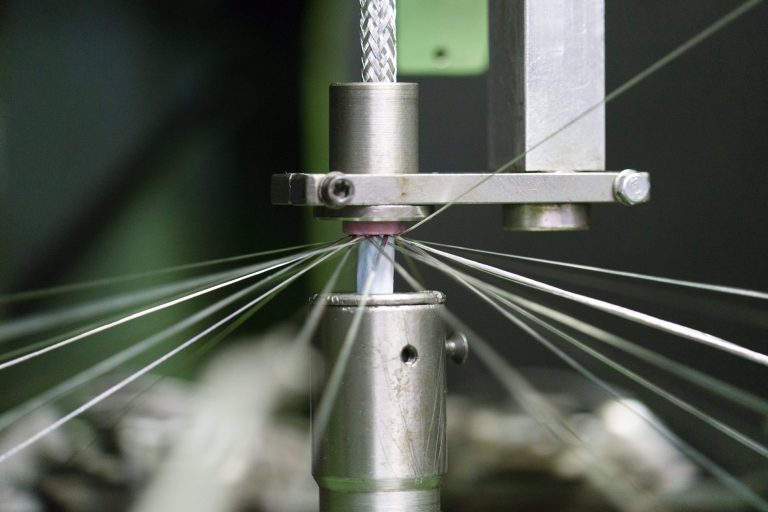
From granulate to plastic coating.
The first production step begins on the core lines. First, plastic and color granules, as well as any additives to protect the plastic later from heat influences, for example, are filled into hoppers, after which the single-screw extruder takes over the next step. Inside the extruder, a plasticizing screw rotates – you can imagine the system a bit like a heated meat grinder. Along this screw, the granules are first added from the hopper and compacted, then melted and processed into a homogeneous mass in the third. Depending on the type of plastic used, the temperature in the extruder can be as high as 240° C, and in some cases as high as 300 °C.
The homogenized melt is conveyed at the end of the screw in the extruder towards the extruder head. There, the copper strand passes through the appropriate die and the melt is formed around it. After the strand receives its insulating plastic layer, it cools in a water bath. The hot insulation is now cooled down to the core of the strand. This enables LAPP to rule out the possibility of the cores sticking together when they are wound onto the iron coils. This process is almost identical for inner and outer core extrusion. After core extrusion, the individual cores are twisted into a flexible core bundle in the stranding shop. The individual cores are inserted at the stranding machines in sequence by color or numerically or alphanumerically. When the plant operator starts the stranding machine after setup, it automatically brings the individual cores together with a rotary motion to form a kind of cord. The finished product is referred to in technical jargon as a wire bundle, stranding or cable core. Stuttgarter Kabelwerke recently acquired a new tube stranding machine for this production step. At 50 meters in length, it is the largest and also the most modern of its kind. “This acquisition was necessary in order to be able to achieve our output of more than 35,000 kilometers of cables per year in accordance with our 2027 strategy at the cable plant. With it, we are increasing our capacity enormously,” says Joachim Schmid.
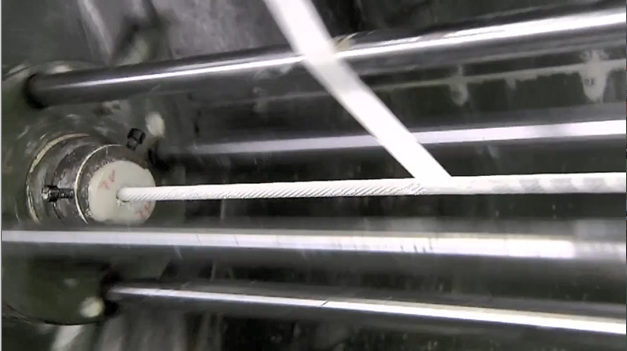
High LAPP standards for all applications
LAPP’s numerous connectivity solutions also include cables and wires that have to meet different conditions and environments. Servo or control cables that need to be protected from electromagnetic influences or from mechanical loads, for example, are given an additional braid before the outer jacket insulation. According to the LAPP standard, this braiding made of tinned copper has a degree of coverage of 80 to 85 percent. Special foils are used for data cables that are only to be protected against electromagnetic influences.
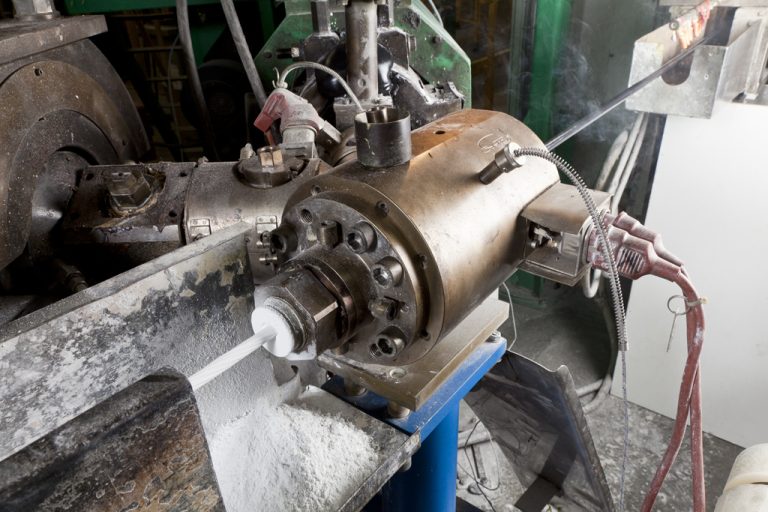
To prevent the braid from damaging the cable core, an inner jacket is added between the core and the braid, depending on the product. Last but not least, the cable is given a protective outer jacket made of plastic – this process is analogous to core insulation. A separate fleece winding, which lies under the jacket, prevents the cable core from sticking together with the outer jacket. Now the cable can be printed – LAPP has a specially defined print legend for this purpose. This serves various legal and normative requirements. For example, it ensures the traceability of the cables and states various specifications that may be relevant for electricians.
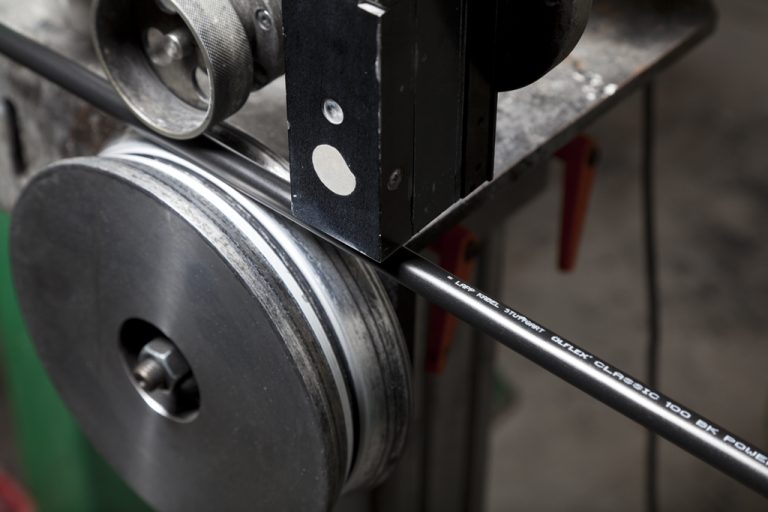
Testing before sale
The cables are wound onto iron drums by machine and are now ready for the final step in the manufacturing process. High-voltage tests, wire-on-wire or wire-on-shield, are performed in Faraday cages. With up to 6000 volts, artificial short circuits are simulated on the cable to put its electrical insulation capability and dielectric strength to the test. After passing the test, the cable is rewound from the iron drum in several pieces onto solid wood or plywood drums and then delivered to logistics warehouses and distribution centers. “The production scraps are then stored separately,” explains Joachim Schmid. “The plastics go into the plastic container and the copper strands into the copper boxes.” The plastic waste can no longer be melted down and reused in cable production – this also applies to residual copper strands. That is why we sell our production waste so that it can be recycled and used elsewhere.