No noise, no spattering metal, no smell of burning – actually you would imagine welding to be different. But not when it comes to a machine from Steigerwald Strahltechnik. In the large chamber, the interior of which can be seen through a window, only a glistening strip of light glides along its path. In less than a minute, it has circled around the shaft of an aircraft turbine, on which a huge blade wheel is mounted. Then the light disappears and the seam between the shaft and the wheel looks like it did before. But that’s an illusion: What had been loosely connected parts are now permanently connected, welded with an invisible electron beam that has penetrated deep into the metal. Admittedly, welding with a laser does look more spectacular, with the red light beam and spattering molten metal in the welding seam. The electron beam, on the other hand, performs its work unobtrusively, although in fact it welds metal blocks as thick as bricks.
WELDS EVERYTHING THAT TURNS
Looking back: In 1952 Karl-Heinz Steigerwald presented the first processing machine with electron beams for industry. In 1963 he founded Steigerwald Strahltechnik GmbH, now part of Global Beam Technologies AG. For the first time, these machines enable workpieces to be welded deep inside, not just on the surface. Karl-Heinz Steigerwald is one of the pioneers who helped achieve the economic upturn in post-war Germany with brilliant ideas – just like Oskar Lapp, who in 1958 invented the first industrially manufactured control cable with ÖLFLEX®, which is now also integrated into the modern versions of Steigerwald’s machines. The electron beam penetrates 150 millimetres into the metal. The heat input is low, which is important for components that should not warp with heat – which is also why the welding process looks so unspectacular.
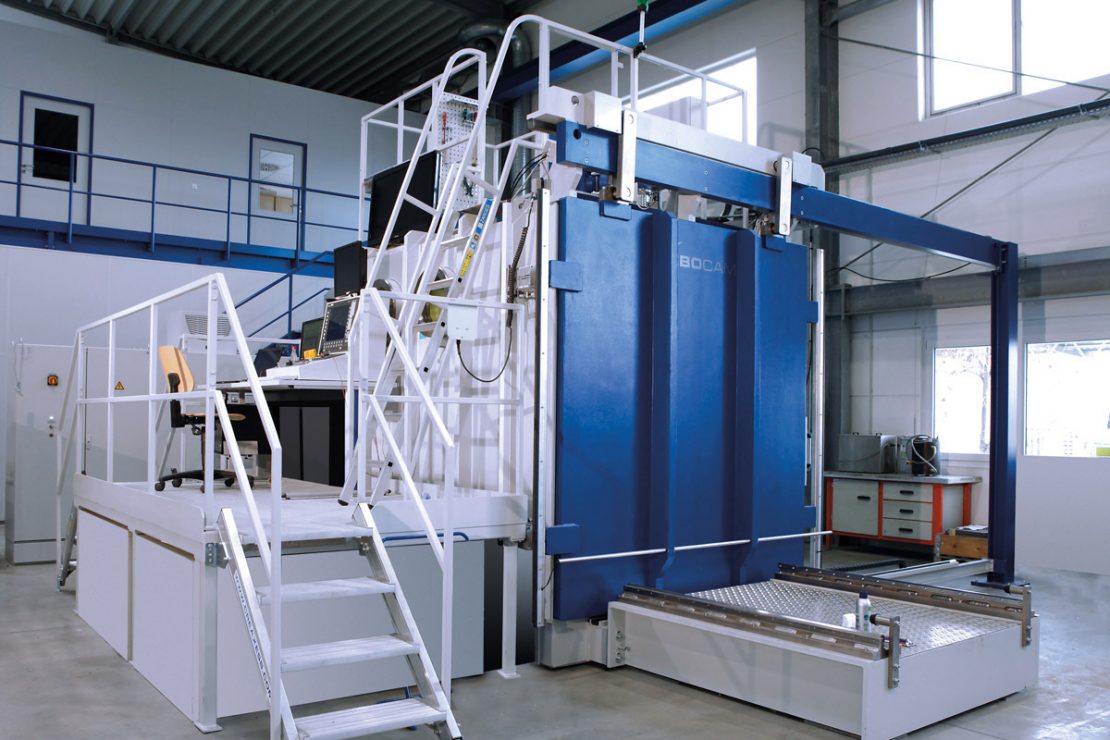
OLDIES FROM THE 1980'S
Given the enormous power of the machines, it is amazing how durable they are. Some customers still operate oldies from the 1980s without major repairs. The electrical connection systems also contribute to this. “I’ve been at the company for 32 years now and still see machines from us that started operation before my time”, says Wolfgang Rudolf, Head of Technology at Steigerwald. This is probably due to the fact that only cables from LAPP are installed – from ÖLFLEX® control cables to UNITRONIC® data cables, connectors and all kinds of accessories. Nobody can say exactly when the collaboration between Steigerwald and LAPP began – perhaps it was in the 1980s. It is well known at Steigerwald, however, that the relationship is fruitful, based on mutual appreciation and that the high quality of LAPP products has been impressive for years. “LAPP’s field service convinced us to rely entirely on its products and we have not regretted it”, says Rudolf. In addition, Steigerwald’s customers, including an increasing number of automotive manufacturers, keep a list of preferred component suppliers that machine manufacturers must comply with. And as the name LAPP appears on many of these lists for cables, it is the most convenient way for mechanical engineers such as Steigerwald to incorporate LAPP everywhere.
PERFECT PLASTIC COMPOUNDS
The quality of LAPP is particularly impressive by virtue of the durability of the products and materials used. In the Steigerwald plants, the cables have to stand up to a lot of punishment. Firstly, the movements of the cable chain in the process chamber, which generally contains two dozen cables, are twice as high in those versions with a moving generator. Current flows through these cables to move the workpiece, for sensors and data – “the entire breadth of the LAPP catalogue”, says Markus Scherer, Head of Purchasing.
However, the biggest challenge is the vacuum in the process chamber. This is necessary because air immediately slows down the electrons so they do not even reach the metal. Cables with unsuitable plastic compounds release gases in a vacuum and become brittle over time. They also have to withstand heat. Although it does not get hot while the chamber is in operation, as there is no heat conduction without air, air enters when the chamber is opened and is abruptly heated. “We select cables with particularly suitable plastic compounds for this purpose”, says Scherer. The hundred or more types of cables, connectors and accessories that Steigerwald regularly purchases from LAPP have proven for many years that vacuum and heat cannot harm them. Neither do the X-rays that impact the cables directly in the cable chain. They occurs when the electrons, deflected by electromagnets as in an old tube television, hit the workpiece at almost the speed of light. Wittig: “We’ve never had problems with LAPP cables”. Certainly not outside the vacuum chambers, where LAPP cables connect control cabinets, control panels, motors and generators.
Wolfgang Rudolf is convinced that the trusting cooperation will last a long time. He is confident that LAPP will continue to provide the accustomed high quality in the future. “The products from LAPP are perfect for Steigerwald Strahltechnik just as they are”.
Video: © SST Steigerwald Strahltechnik: Solutions for the Aerospace Industry