Five different plastics are primarily used in the area of cables and connection solutions: PVC (polyvinyl chloride) is an all-rounder that can be easily modified with additives and is characterised above all by its flame resistance and flexibility. TPEs (thermoplastic elastomers) are very elastic and resistant to media. Polyamides, with their temperature resistance, are used for UL certifications and in the connector sector, while radiation-crosslinked polyethylene (PE) is used for photovoltaics and rail vehicle products. LAPP has around 40,000 products in its portfolio. The leading provider of integrated solutions and branded products in the field of cable and connection technology has released over 400 different plastic compounds for this purpose. In fact, there are countless variants around the world, depending on the area of application.
Plastics consist of polymers and additives and are usually obtained from petroleum products. They consist of long carbon chains and are particularly versatile due to their properties (non-rusting, waterproof, extremely durable, flexible, insulating). For cable sheathing, for example, it is particularly important to optimise meltability (thermoplastics) for use in extrusion as well as the special properties of the cooled and solidified sheathing material. Research is focussing on how these properties can be influenced and how the optimum material can be found for the respective cable. Additives play an important role here: the range of properties can be extended by combining polymers with suitable additives. Skilfully selected and introduced additives protect the jacket materials against abrasion, facilitate processing in melt form, make the material more resistant to thermal and UV influences or improve flame retardancy. Both IKT and LAPP are constantly producing and testing new compounds in order to achieve an optimised plastic. Another constant goal of materials technology is the predictability of material behaviour in use. To this end, research is being carried out into the transferability of time-lapse test conditions to practical use. The flow properties are also determined using complex measurement methods. This is very important before extrusion, for example, in order to prevent instabilities in production. However, the IKT also conducts detailed research into which additives can improve a certain behaviour. For flame retardancy, for example, special fillers are used that absorb heat but at the same time impair the flow properties. Radical scavengers are used for UV protection and waxes optimise the flow behaviour in terms of viscosity.
The IKT’s research spectrum is huge. Research is currently being carried out on the mechanical recycling of the bioplastic PHB. Here, suitable additives are added in the twin-screw extruder and react with the PHB. Another research project is focussing on the increasing demand for high-performance plastics, particularly in the field of electromobility. Stabilisers are used here to improve media, hydrolysis and temperature resistance, but these are difficult to recycle, and in practice the addition of glass fibres often worsens the ageing properties. The IKT is working on the synthesis of a new type of stabiliser based on high-polymer organic amines and the development of a clever processing strategy for the new stabilisers.
In order to make a machine, tool or manufacturing process more efficient, its condition must first be described sufficiently. Sometimes it is necessary to invent suitable measuring equipment and methods first. In order to be able to predict the behaviour of the machine and tool in the process, research is being carried out at the IKT on model-like mathematical descriptions of the respective process that can be used as universally as possible in order to be able to predict this realistically – and better than in commercial simulation programs. Processing methods and plastic selection are therefore important factors. In cable production, the plastic is usually processed by extrusion. A high viscosity is required here. The IKT is therefore not only researching high-performance single-screw extruders, but also the modification of polymers to achieve high viscosities.
In contrast, the injection moulding process is used in the production of connectors. This requires precise cavity moulds, a rather low viscosity and particularly fine structures. To this end, the IKT is conducting research into the material efficiency of thermally conductive plastics or the measurement of flow properties within the machine (keyword “Industry 4.0”).
A plastic product can be made more efficient, e.g. by fulfilling several functions at the same time or by fulfilling the previous function under more demanding boundary conditions. To do this, the product condition must first be determined and, if necessary, research into measuring equipment and methods must be carried out. With the help of material laws, research is carried out into the predictability of product behaviour, especially for predicting service life under different operating conditions. The component behaviour is simulated with the aid of calculations and validated with selected tests. In the case of cables, this involves questions about the environmental conditions to which they are exposed. Oil and UV resistance or how many alternating bending cycles a cable can withstand in a drag chain without damage. LAPP’s top priority is to maximise the service life of its products, which makes a major contribution to sustainability.
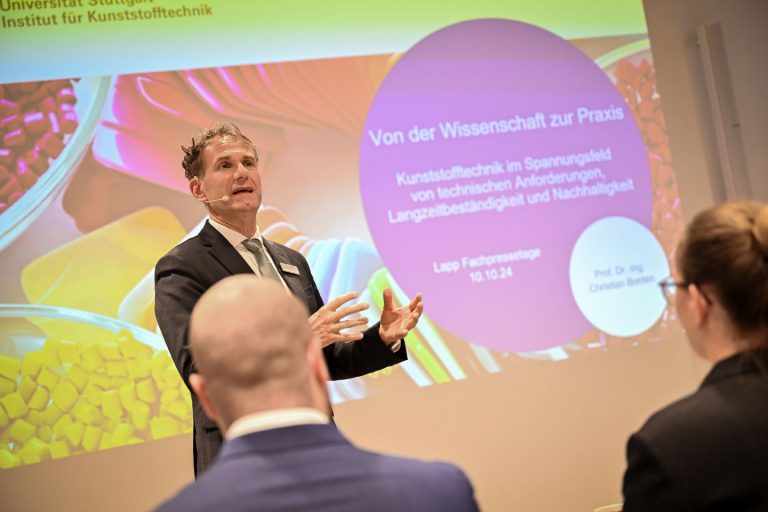
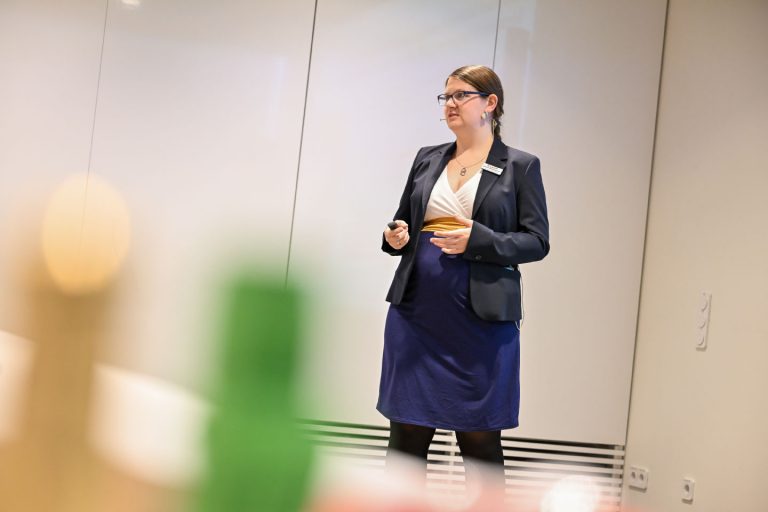
For LAPP, the IKT is a competent partner for all plastics topics. The institute not only conducts basic research, but also application-orientated development projects. It covers all areas of plastics technology, from the raw material to the component and its service life, and has a comprehensive understanding of the various areas such as compounding and processing. LAPP has also been involved in the optimisation of materials for decades and has extensive knowledge of plastics. The company knows and understands the entire value chain, from the raw material to the end product, because customised solutions can only be realised through the perfect interaction of all components.
Dr Silvia Lajewski, who wrote her doctoral thesis at the IKT on the above-mentioned topic of recycling PHB, is now the global contact for plastics development topics at LAPP. This makes her the “top chef” for customised plastics. Until recently, LAPP was primarily a plastics processor and purchased the required compounds from large, well-known manufacturers. For a good year now, LAPP has been operating its own compounding plant with two production lines to manufacture the PVC compounds required as granulates, primarily for the production sites in Asia. Another line mixes special compounds such as halogen-free cables for fire protection. By strengthening compounding at LAPP, expertise in the composition of the plastic compounds used is growing. This opens up new possibilities for the use of special compounds for special cables, but also generally for an optimal choice of materials for all cables. LAPP is thus venturing – backwards along the value chain – into a new branch of industry with completely different challenges for personnel and equipment than in cable production.
But LAPP’s vertical integration and expertise is also enhanced by its own radiation crosslinking facility in India. In addition, there are worldwide test and inspection centres. For example, a fire test laboratory was recently opened at the Camuna Cavi production site in Italy to test fire properties in accordance with prescribed standards. Other test centres for mechanical tests (tensile strength, temperature resistance, flexural strength, etc.) and chemical analysis are located in Stuttgart, Korea, China and the USA. LAPP has also founded a “Tech Council Compound”, where 30 experts from all over the LAPP world meet every two months to discuss specific projects. Dr Susanne Krichel, responsible for global research and advance development, is pushing the development of sustainable products. LAPP’s developers are currently working on bio-based plastics for EPIC® connectors and SKINTOP® screw fittings.